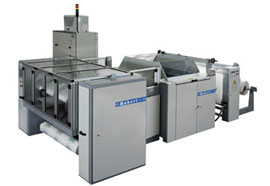
Roll to Roll 130/200E
Specialistic line for the production of industrial bags pre-cutted and wolded. Packing: bags winded on carton core dia.76mm. Winding unit in continuous on two station, with automatic tearing and sticking of the fi lm on the new core. Automatic discharge of the roll at the end.
Technical characteristics:
TECHNICAL SPECIFICATIONS | roller to roll 130 E | roller to roll 200 E |
Max bag with | 1300 mm | 2000mm |
Min bag lenght | 400 mm | 400 mm |
Max bag lenght | 20.000 mm | 20.000 mm |
Min film thickness | HDPE 0.008 mm | HDPE 0.008 mm |
Max film thickness | LDPE 0.100 mm | LDPE 0.100 mm |
Max mechanical speed | 230 cycles/min | 150 cycles/min |
Max speed film | 150 metres/min | 150 metres/min |
Diameter of carton core | 76mm (3”) | 76mm (3”) |
Max diameter of end reel | 400mm | 300mm |
Max. roll width | 1300mm | 2000mm |
Min. roll width | 400mm | 400mm |
Total installed power........................ | 15 Kw | 18 Kw |
Compressed air consuption.............. | 150lt/min | 150lt/min |
Optionals:
- OP 33: Double welding unit for bags with sides welding
- OP 24: Optical film guide
- OP 39: Automatic feeling for carton core
- OP 3: Device for printed film
- OP 34: Self centering reel holder
- OP 20: Perforation bar